Test and assembly automation are key factors in bringing about higher quality manufacturing of products, but also in allowing people working in production to achieve a greater meaning in their work through more varied job functions, increased safety, and improved work ergonomics. We believe these are issues we can tackle in true JOT fashion – Just On Time.
The discussion around automating manufacturing processes has evolved significantly from what it was when automation was first brought to the table. And with the rapid development of automation solutions, the concept of automation itself has to be continuously updated. Take for example our ANT Plant microfactories, a quick-to-adopt automation solution with advanced manufacturing robotic cells, which are essentially a new way to think about the entire delivery process.
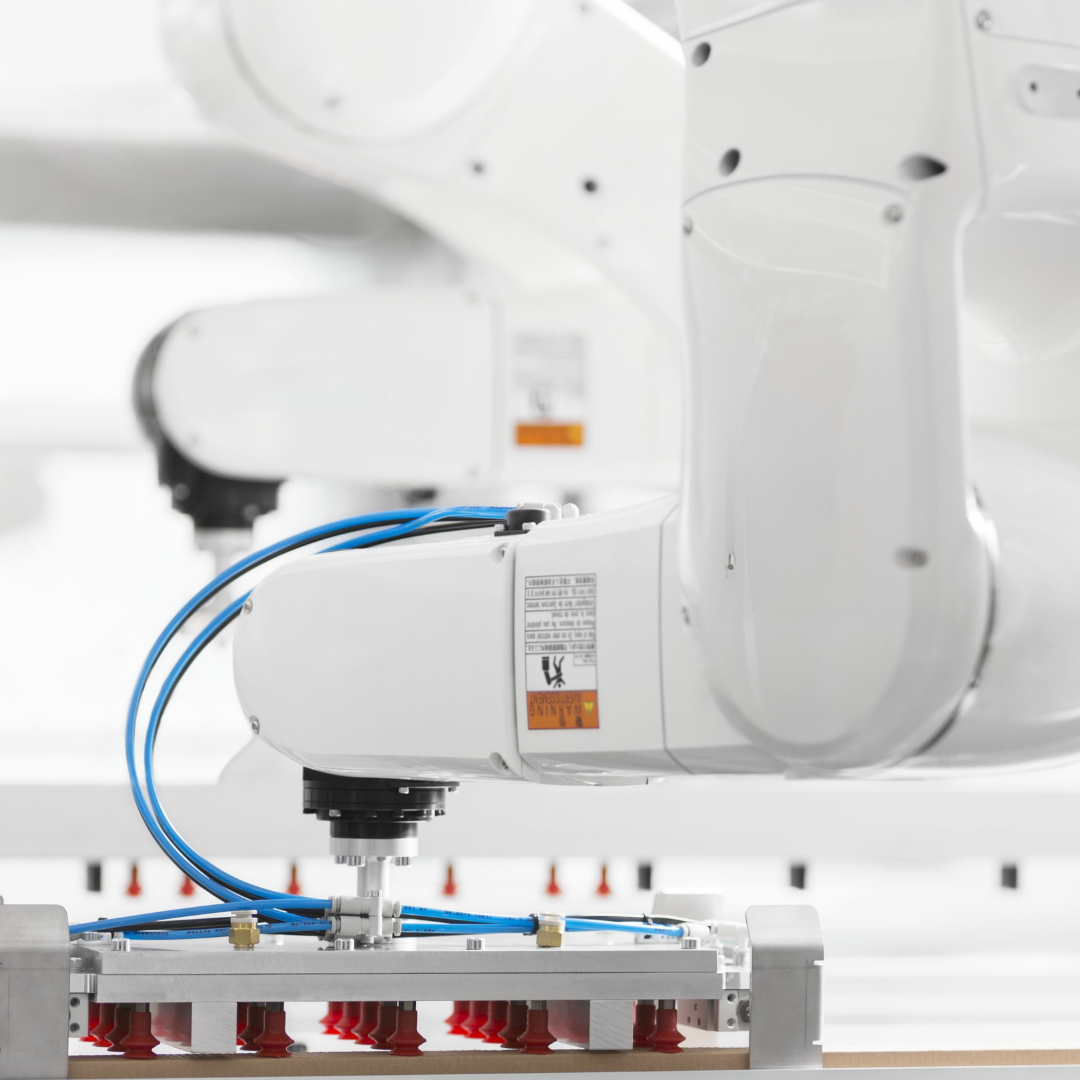
%20battery%20test%20solution/battery-cell-tester-highlight-5.png?width=800&height=472&name=battery-cell-tester-highlight-5.png)
The development has been so dramatic that what previously constituted simple processes and mechanical tasks has expanded to include e.g. smart production systems, AI-based solutions, and even predictive manufacturing solutions. All in all, automation has evolved to a place where it enables local jobs and improves job quality.
Still, even as automation has come to be seen as an enabler, there are warped expectations and perceptions of what the cost of investment in automation is. The perception becomes exceedingly warped when talking about industries with extremely high production volumes, such as those manufacturing e-vehicles and energy storage batteries.
Fortunately for you, we can highlight some of the advantages of investing in battery test and assembly automation. In a nutshell, some of the main reasons to invest in battery test and assembly automation are
- 100 % verifiable tracking throughout the production line
- Lower lifecycle costs
- Improved safety
- Increased speed and consistency in production
Leveraging these advantages through automation is possible at any point in your production cycle. For the best results, though, the earlier automation can be brought into the product design process, the better the end product, as well as cost efficiency, but we’ll get into that later.
Remember, however, that these are just some of the reasons – we’re more than happy to hear more about your needs, if you care to share!
Turn battery production challenges into your competitive edge
Battery manufacturing has plenty of challenges, all of which can hinder production in different ways. As it happens, automation is such a multifaceted solution that its different aspects are perfectly matched to solving these challenges and even give you an advantage.
One of the – literally – biggest challenges in battery test and assembly is the range in size and weight of battery modules. As the biggest modules can weigh in at tens and hundreds of kilograms, manual testing and assembly get really cumbersome, often requiring specially designed lifting systems. In addition to the required extra equipment, the handling of heavy loads in large, varying shapes is a constant health and safety hazard, with added poor work ergonomics in the manual handling of the modules.
Test and assembly automation works wonders in addressing these issues however, an automated test and assembly line takes care of all the heavy lifting for you. This means no more heavy lifting with specialized rigs or worrying about dropping heavy and fragile battery packs. An investment in test and assembly automation thus also becomes an investment in your employees’ well-being, along with increased job meaningfulness. And why would you say no to that?
Another issue with battery test and assembly is quality assurance and tracking. It’s a given that when humans work, there’s also room for human error. Mislabelling, mishandling, any other mishap – something will happen sooner or later. Humans also have a limited capability for certain tasks that require incredible accuracy, e.g., measuring an object’s dimensions or temperature quickly and accurately.
%20battery%20test%20solution/battery-cell-tester-highlight-2.png?width=800&height=509&name=battery-cell-tester-highlight-2.png)
Any one of these issues influences a manufacturing operation greatly – if not already on the production line, then after being delivered to your customer or even to the end customer. And by then, any small issues in quality – faulty battery packs, damaged battery modules, smallest impurities, and so on – become hefty costs either through compensation, repair or even massive-scale callbacks. Not to mention, defects in battery cells, packs or modules can be hazardous to their operating environment, and any possible damage at that point isn’t measured in monetary terms.
With an automated battery test system and assembly line, however, you get rid of these challenges altogether. Not only are automated test units able to handle individual battery cells, battery packs, and even battery modules with supreme accuracy, they are also capable of conducting performance tests and calculations at superhuman levels, tirelessly around the clock.
This means automated testing lines are able to optimize battery packs and modules on their battery cell level to achieve maximum capacity and minimum downtime, allowing you to deliver battery modules with uniform performance and consistency like no other.
Automated test and assembly with JOT’s solutions also means using machine vision that can measure and detect even the slightest abnormalities in battery cell or module dimensions. Throw in dedicated temperature sensors that detect even minimal temperature changes, and you have a combination that ensures uniform performance and consistent high quality. These solutions, in turn, make it possible to react to possible battery malfunctions before an accident happens.
Another thing an automated testing line can detect earlier is the rising temperatures caused by chemical reactions, which at first can be minimal and undetectable by a human handler. But the earlier a malfunction can be detected, the more time there is to react and the safer the production line becomes by proactively minimizing any potential risks.
The added benefit, of course, just as with detecting other faults, is to be able to avoid assembling and shipping faulty battery modules that, down the line, cause large callbacks and other additional costs, and to ensure your production downtime is at a minimum.
The price is right – and decreases relatively the more you manufacture
Like in any manufacturing business, the relationship between the cost of production and the quality of products should be optimized. Thus, any large acquisition of new production equipment and infrastructure can seem initially too costly to invest in.
But, instead of looking at the initial lump sum, your focus should be on what’s left in your bottom line – and how not investing in test and assembly automation can diminish your bottom line.
So let’s put things into perspective: a single battery module can contain hundreds of single battery cells; thus, manufacturing thousands of battery modules equals millions of single battery cells. As a result, investing in an automated battery test solution means your cost per tested battery cell is, at the very least, calculated in cents.
This means that, over time, your ROI pertaining to battery test and assembly automation keeps on getting better and better. And once you factor in the potential costs that repairing or recalling faulty battery modules brings, the more you get out of your investment.
Just don’t think we haven’t got your bottom line in mind!
JOT’s automation solutions also have an advantage that keeps serving your bottom line – and that is longevity. As in any electronics manufacturing, battery manufacturing evolves constantly, product dimensions vary, and components change. With JOT’s automated Battery Test Solution, 90% of the initial investment is for the infrastructure, and the rest is customized parts.
This means, in the future, when you need to change or upgrade your test or assembly lineup to be compatible with your new products, you only need to invest 10% of the initial investment to customize your pre-existing production platform.
With that minimal investment done, your waiting time is counted only in weeks instead of months, which happens when you start production from the ground up. After just a matter of weeks, you’re up and running again with an updated product test and assembly line, saving you time and – again – money.
There really is more to automated battery testing and assembly
If what you’ve just read hasn’t yet convinced you to invest in battery testing and assembly automation, let us know! We’d sure like to hear why that is. We are also ready to discuss more with you about the other benefits battery testing and assembly automation can offer you. So get in touch!